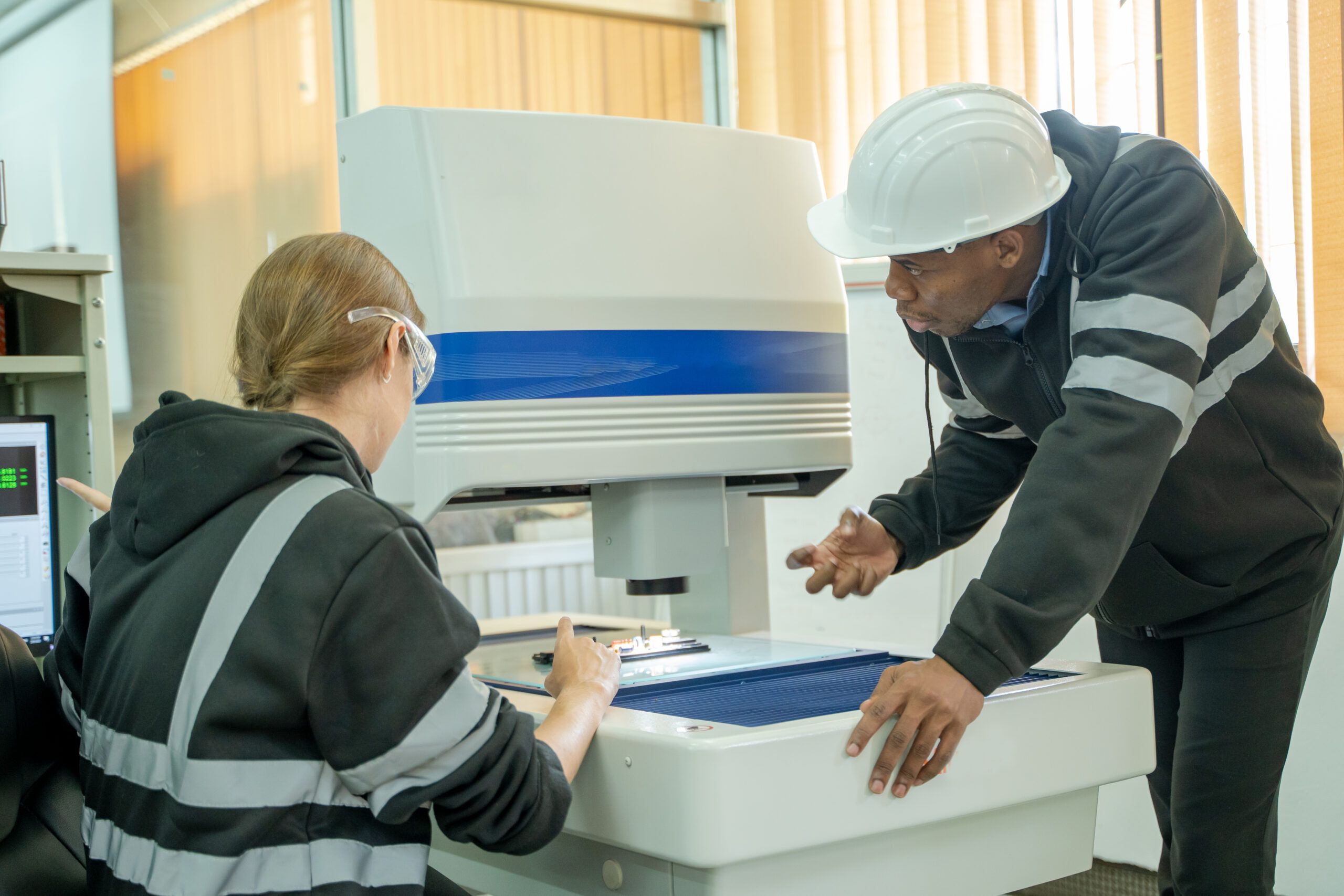
The foundation of quality control
Quality control in the restoration of geometries is a fundamental pillar in many industrial sectors, especially where precision is non-negotiable. The process begins with a thorough analysis of the technical specifications of the component under examination, asking crucial questions about tolerances, materials, and measurement methodologies.
The choice of measuring tools plays a key role, determining the accuracy and reliability of the assessments made. At this stage, the expertise in correctly interpreting the specifications and selecting the most appropriate tools is essential for establishing the basis of effective quality control.
READ ALSO: Ceramic coatings for tools and specific geometries
Data interpretation and informed decisions
Once the measurement data are collected, the next step in quality control involves the analysis and interpretation of this data. This phase raises important questions about data variability and how this can influence the final decisions.
It is crucial to understand how fluctuations in the data can reflect real variations in the piece or mere artifacts of the measurement techniques. The ability to distinguish between these two aspects and to make decisions based on accurate analysis is fundamental to ensure that the parts are restored within the required tolerances and comply with quality standards.
READ ALSO: Roller for wear-resistant coatings: an innovative solution for protection and industrial efficiency
Techniques for geometry restoration
The heart of the quality control process in the restoration of parts is the choice and application of the most suitable restoration techniques. The correct technique selection depends on a variety of factors, including the type of material, the nature of the damage, and the specific objectives of the restoration.
Key questions at this stage include assessing the effectiveness of different techniques for specific geometric configurations and their impact on the durability and performance of the restored component. The goal is to find an optimal balance between correcting imperfections and maintaining or improving the original properties of the material.
READ ALSO: Corrosion: why do mechanical parts corrode?
The expertise of the staff: a key factor
Finally, quality control and geometry restoration significantly depend on the training, experience, and skills of the involved personnel. Questions at this stage concern how to ensure that the staff is adequately prepared to face the technical challenges of the process and how continuous skill updating can contribute to quality improvement.
Ongoing training and adjustment to new technologies and methodologies are essential to maintain high quality standards and to effectively meet the constantly evolving needs of the industry.
This article has explored the various aspects and challenges of quality control in the restoration of geometries, highlighting the importance of a thorough understanding of technical specifications, precise measurement techniques, decisions based on accurate data, and highly qualified personnel.
Considering the complexities and challenges discussed in geometry restoration and quality control, it is crucial to rely on industry experts who possess the technical competence and practical experience to manage these processes with precision. An excellent example in this context is Paganoni, a company that stands out in the industrial landscape for its dedication to offering high-quality solutions in the field of precision mechanics.