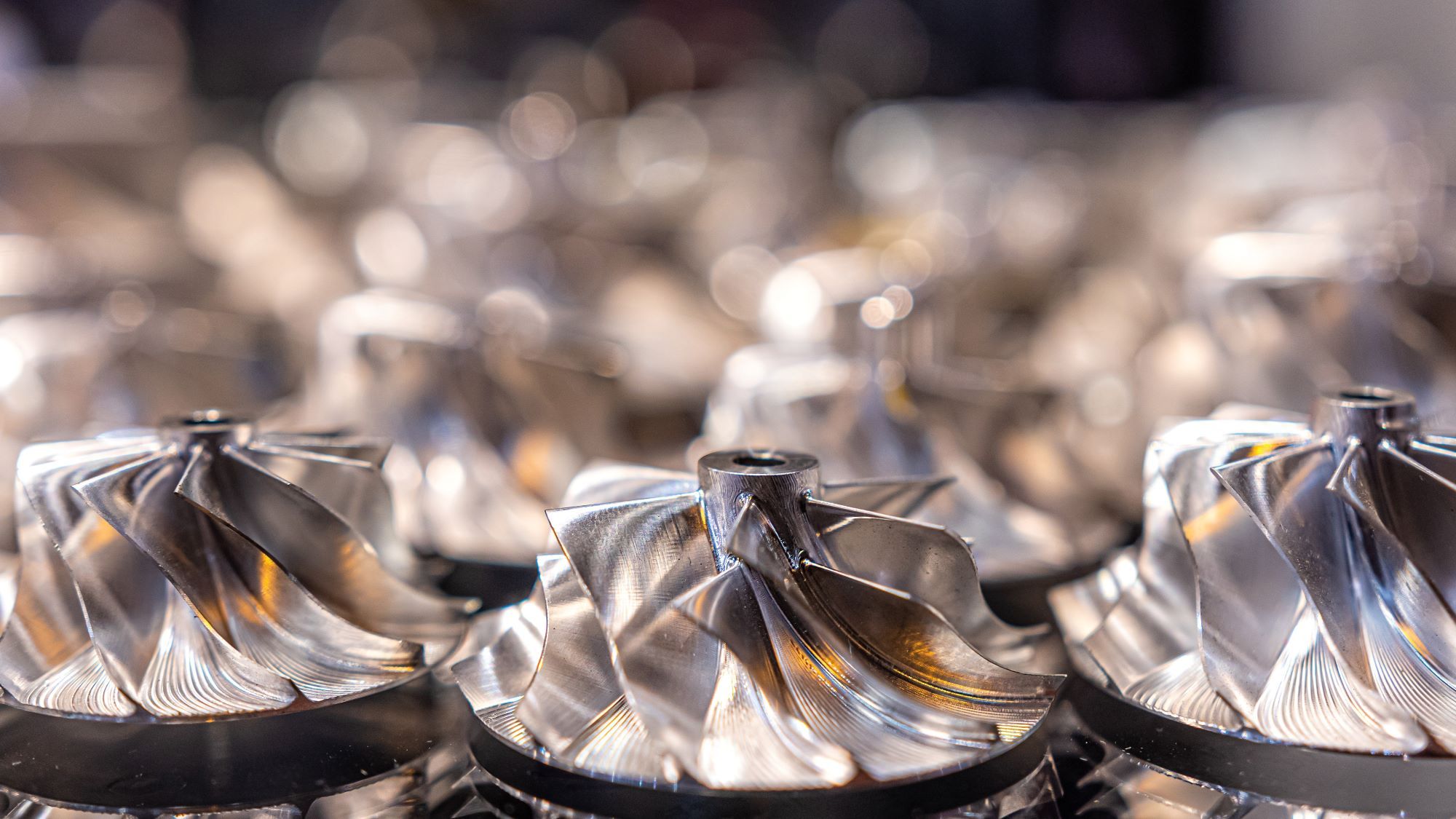
Which Coatings to Choose for Different Metal Alloys? A Complete Guide
In the world of wire drawing and metal processing, selecting the most suitable coating for each metal alloy is not just a technical decision — it’s a strategic choice that impacts the lifespan of components, production efficiency, and the quality of the finished product. Each metal presents specific chemical and physical properties that require tailored solutions to reduce wear, friction, corrosion, and production slowdowns.
Stainless steel, copper, aluminum, high-strength alloys, and specialty metals all pose different challenges when it comes to contact with drawing capstans, rollers, pulleys, and cones. This is where advanced technical coatings — such as those developed by Paganoni — come into play. These coatings make it possible to increase productivity, lower operating costs, and ensure high-quality output.
In this technical guide, we’ll explore:
- The key characteristics of the most common metal alloys
- The most frequent issues in metal-to-coating interaction
- The most effective industrial coatings for each type of alloy
- The technical criteria for making the right, long-lasting choice
Understanding Metal Alloys to Select the Right Coating
The first step in identifying the most suitable surface treatment is to fully understand the specific properties of the metal alloy being processed. Metal alloys used in wire drawing behave differently under mechanical stress, chemical exposure, abrasion, and temperature variation. These factors directly influence the performance of the coating, and consequently, the efficiency of the production process.
The most commonly used alloys include:
- Carbon steel: offers good tensile strength but is prone to abrasive wear and oxidation.
- Stainless steel: delivers excellent corrosion resistance, but has a harder surface that increases friction.
- Copper and copper alloys: highly ductile and conductive, but vulnerable to galling and surface deformation.
- Aluminum: appreciated for its workability and lightness, but has a soft surface that’s easily scratched or torn.
- Nickel alloys: ideal for high-temperature applications and chemically aggressive environments.
Each metal presents a unique combination of critical factors. Selecting a coating that’s too hard can lead to excessive friction, while coatings that are too soft may fail to protect components over time. Both situations can result in premature wear, downtime, and a decline in production performance.
To avoid costly mistakes and ensure optimal results, get in touch with the Paganoni technical team: we’ll help you identify the most compatible coating for your specific metal alloy and wire drawing process. Request a personalized consultation now.
Coatings for Steel: Managing Abrasion and Oxidation
Carbon steel and stainless steel are among the most commonly used alloys in industrial wire drawing. Their popularity stems from their high mechanical strength, versatility, and cost-performance ratio. However, both materials pose significant processing challenges, especially when it comes to abrasive wear, overheating, surface oxidation, and in the case of stainless steel, higher hardness and friction.
With carbon steel, the primary issue is its high rate of abrasion, caused by friction between the wire and mechanical parts such as capstans, cones, and rollers. Exposure to certain operational environments can also lead to localized oxidation, accelerating the deterioration of components. To tackle these problems, Paganoni recommends high-wear-resistant coatings such as Wolside® or Coldside®. Both are based on special tungsten carbides, applied using advanced techniques to create extremely hard and compact surfaces. In particular, Wolside®, thanks to hot fusion and its ultra-dense structure, ensures long-lasting durability even in extreme conditions, while minimizing friction and enabling higher production speeds.
Stainless steel, on the other hand, while offering excellent corrosion resistance, presents challenges related to its high surface hardness and friction coefficient. In these cases, a coating is required that can reduce sliding resistance without compromising surface finish quality. This is where Kerblack® proves ideal: composed of chromium oxides, it delivers intrinsic lubrication that limits contact damage and reduces heat buildup. The result is extended component life and better surface quality on the drawn wire.
Properly matching the coating to the type of steel is therefore essential to maximize productivity and control maintenance costs. A poor choice can compromise the entire production cycle, leading to machine downtime and significant economic losses.
Are your components working with demanding steel alloys? Contact us for a free technical assessment and discover which coating can truly make a difference. Request your analysis now
Copper and Light Alloys: Protecting Soft Surfaces from Galling
Copper and its alloys (such as brass and bronze), along with aluminum, are widely used for the production of wires and conductors due to their high electrical conductivity, ductility, and lightweight properties. However, these same features make them extremely vulnerable to deformation, surface scratches, tearing, and galling during the wire drawing process. For this reason, choosing the right coating for the components in contact with these metals becomes even more critical.
One of the most challenging issues is galling — an unwanted adhesion between the surface of the metal and the component, which can lead to process interruptions, damage to the wire surface, and even premature failure of the coating. To prevent this, Paganoni recommends the use of highly lubricating and non-stick coatings such as Kerblack® and Niksint®.
Kerblack®, made from chromium oxides, provides an exceptional combination of hardness and smoothness, making it particularly effective when working with copper and brass. Its ultra-low friction coefficient minimizes metal adhesion and prevents the formation of deposits or surface marks on the wire.
For applications involving annealing tubes or corrosive environments, Niksint® — a nickel-based coating — is the preferred choice. Known for its outstanding chemical resistance, it performs exceptionally well even under demanding thermal cycles. Its uniform structure also ensures a clean and consistent surface finish, ideal for softer metals.
In dry drawing processes for copper and aluminum wires, Paganoni coatings help significantly reduce downtime, improve production continuity, and ensure consistent quality control of the processed wire.
Working with copper, brass, or aluminum and need to prevent galling and surface damage? Rely on our expertise to identify the most suitable coatings for your production line. Request personalized information now
Nickel Alloys and Extreme Environments: When Chemical Resistance Matters
Nickel alloys are widely used in the most demanding industrial settings: chemical plants, high-temperature systems, high-salinity environments, or harshly corrosive conditions. These materials are chosen not only for their mechanical strength, but more importantly for their exceptional corrosion resistance and thermal stability. However, processing these metals within wire drawing cycles requires specialized coatings capable of delivering long-term protection without compromising precision or operational continuity.
In such scenarios, components that come into direct contact with the metal — such as tubes, rollers, capstans, and drawing rings — must be treated with coatings that can withstand not just wear, but also chemical attack and thermal deformation. Niksint®, developed by Paganoni, is specifically engineered for these conditions. Made from a uniform layer of high-purity nickel, it acts as a robust protective barrier against oxidation, acidity, and the thermal cycling commonly found in these installations.
In addition to its chemical resistance, Niksint® is also valued for its surface uniformity, which reduces the risk of microcracks or build-up, ensuring a smoother and more predictable wire drawing process over time. This feature is particularly important in inline annealing systems, where nickel alloy wires must endure critical phases of rapid heating and cooling.
Another key benefit is the coating’s adaptability to specific production requirements. Thanks to its excellent stability, Niksint® is suitable even for partial coatings, such as targeted areas on tubes or customized components. This makes it possible to optimize performance while reducing costs.
Are you operating in aggressive environments or working with high-performance nickel alloys? Discover the advanced applications of Niksint® and benefit from expert technical guidance. Contact our team today for a tailored evaluation of your process.
How to Choose the Right Coating: Technical Criteria and Tailored Solutions
Choosing the optimal coating cannot be based on a general rule or personal preference — it is a technical process that requires a detailed analysis of the operating conditions, the materials involved, and the production goals. In other words, to ensure high performance and long-term durability, every mechanical component must be custom-coated with a treatment compatible both with the metal alloy being processed and the type of wire drawing operation (dry, wet, multiwire, high-speed, etc.).
The key selection criteria include:
- Chemical composition of the alloy: each metal reacts differently to heat, friction, acids, or lubricants.
- Type of mechanical stress: abrasion, impact, galling, torsion.
- Operating environment: humidity, high temperatures, corrosive agents.
- Component type: capstan, cone, tube, roller, pulley, dancer, etc.
- Required precision level: surface finish, dimensional tolerances, roughness (Ra).
To effectively manage this complexity, Paganoni adopts a consultative, technically driven approach. We don’t offer generic coatings — we analyze the client’s production environment, critical issues, materials in use, and process parameters. Only after this evaluation do we recommend the most appropriate solution from our specialized coatings: Wolside®, Coldside®, Kerblack®, Kersint®, or Niksint®.
This approach not only maximizes component performance, but also extends service life, reduces machine downtime, and lowers maintenance and replacement costs. It’s a strategic decision that brings measurable value over the medium to long term.
Want to avoid trial and error and identify the most effective coating for your equipment and metal alloys? Request a free technical consultation with our expert team today.