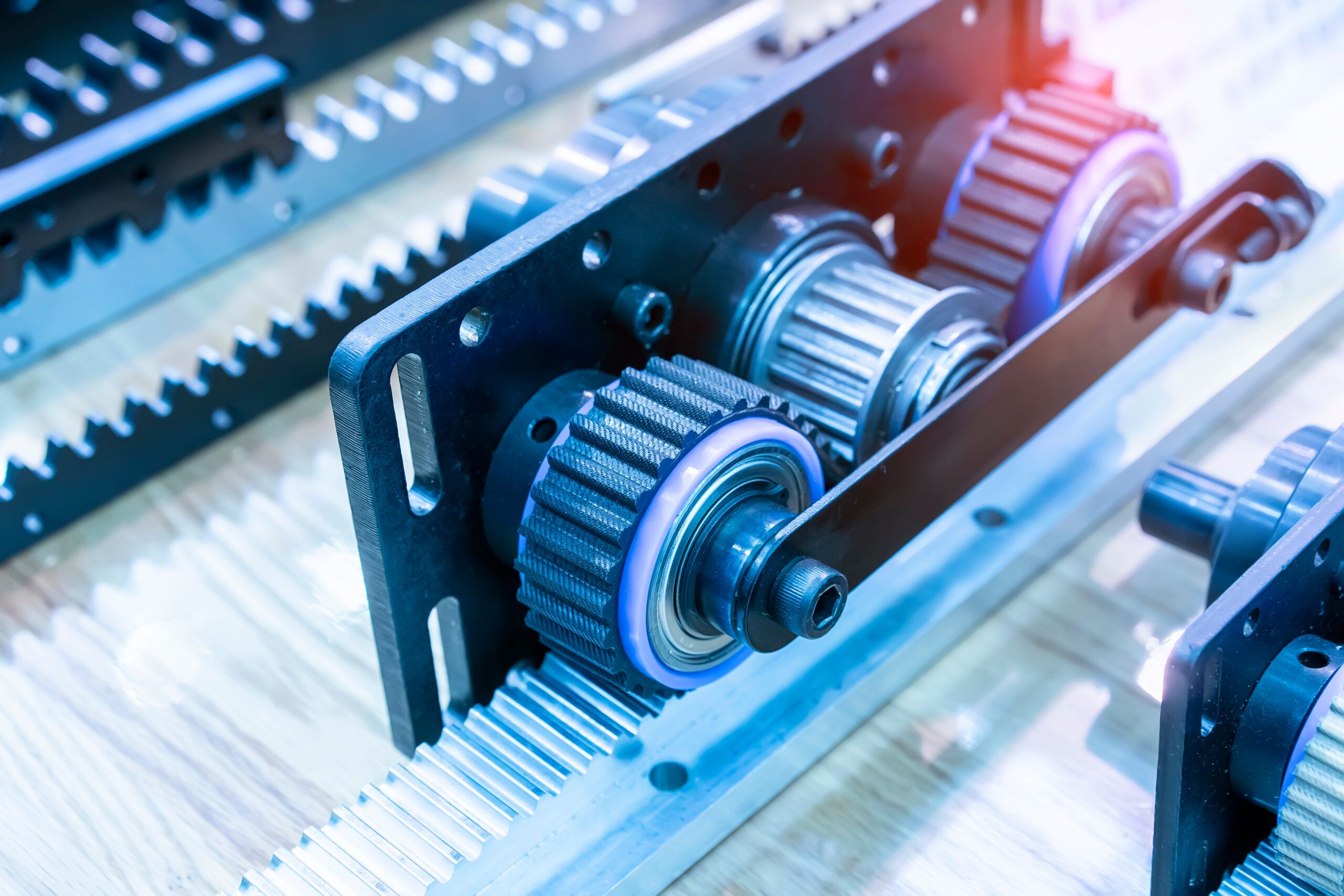
How to Prevent Downtime in Wire Drawing with the Right Coatings
The Importance of Preventing Downtime in Wire Drawing
In the wire drawing industry, every minute of downtime represents a significant financial loss and a barrier to business competitiveness. Whether planned or unplanned, downtime negatively impacts productivity, causing delivery delays, increased operational costs, and a decrease in customer satisfaction. Preventing these interruptions is therefore a strategic priority for all companies operating in the metal wire processing sector.
The main causes of downtime in wire drawing are often linked to excessive wear of components, high friction during wire passage, or sudden breakages caused by mechanical and thermal stress. Failing to act promptly on the progressive wear of capstans, cones, and pulleys can result in far more serious and costly damages. Thus, it is essential to adopt a proactive approach, based on prevention through the use of high-performance materials.
Today, high-quality anti-wear coatings offer a concrete solution to avoid extended production stoppages. Choosing coatings such as Wolside®, Kerblack®, Kersint®, or Coldside® can significantly extend the operational life of critical components, reducing the frequency of extraordinary maintenance and improving the overall efficiency of the plant. Optimized component lifecycle management not only results in smoother production processes but also provides a substantial competitive advantage in the global market.
Investing in downtime prevention means ensuring continuous production, optimizing costs, and maintaining high-quality standards. It is a decision that pays off both in the short and long term.
Would you like to effectively prevent downtime in your wire drawing line? Contact the Paganoni team today for a dedicated and personalized consultation!
The Impact of Wear on Wire Drawing Components
In the metal wire drawing process, components such as capstans, cones, pulleys, and wire guide rollers are constantly subjected to intense mechanical stress. The continuous friction generated by the wire passage, combined with high pressure and temperature variations, inevitably accelerates the phenomenon of wear. As these components begin to deteriorate, resistance to the wire passage increases, leading to a loss in the quality of the finished product and compromising the stability of the entire production line.
The progressive wear of contact surfaces results in a higher amount of energy required to maintain production, causing an increase in energy consumption and greater stress on machinery. Moreover, the risk of sudden breakages or line blockages becomes increasingly real, leading to unplanned downtime that heavily impacts production timelines and costs.
A worn component not only limits the machine’s performance but can also cause structural defects in the drawn wire, compromising the quality of the finished product and increasing the amount of waste. For companies, this translates into both direct and indirect financial losses, potentially damaging long-established business relationships.
Uncontrolled wear is therefore a silent enemy of productivity. Preventing damage caused by wear requires the selection of technologically advanced anti-wear coatings, capable of maintaining optimal mechanical characteristics over time and ensuring long-lasting operational durability, even under extreme working conditions.
Don’t let wear compromise your productivity! Contact Paganoni today and discover the ideal solution to protect your wire drawing components.
Choosing the Right Coating: Wolside®, Kerblack®, Kersint®, Coldside®
Selecting the right coating for wire drawing components is a strategic decision that can make the difference between continuous production and frequent downtime. Not all coatings deliver the same performance: to ensure wear resistance, friction reduction, and operational longevity, it is essential to rely on technologically advanced solutions such as those developed by Paganoni.
Wolside® represents the top-tier choice for those seeking high impact resistance and a low coefficient of friction. Thanks to its hot-fusion process involving tungsten carbides and rare minerals, this coating guarantees exceptional durability even in the most demanding wire drawing cycles. Kerblack®, based on chromium oxide, is the ideal solution for dry drawing applications, where drastically reducing friction and protecting components from galvanic corrosion is critical.
For extreme environments where chemical resistance and thermal stability are decisive, Kersint®, the super-sintered ceramic material based on zirconium oxide, offers unparalleled performance. Finally, Coldside® stands out as the perfect solution for the recovery of worn capstans and pulleys, thanks to its excellent adhesion to finished parts and outstanding mechanical strength.
Choosing the right coating means proactively addressing the key vulnerabilities of the wire drawing process. With Paganoni’s materials, every component becomes a productivity ally, capable of withstanding long work cycles without degradation.
Would you like to know which Paganoni coating is best suited to your needs? Contact us now to receive a personalized technical consultation!
YOU MIGHT ALSO BE INTERESTED IN: Coating Technologies for Wire Drawing Components: Innovation and Performance
How Paganoni Coatings Improve Production Efficiency
In the competitive world of industrial wire drawing, improving production efficiency is not just an advantage—it is a necessity. Paganoni’s anti-wear coatings play a crucial role in this process, ensuring superior component durability and consistent performance over time. By adopting high-performance materials such as Wolside®, Kerblack®, Kersint®, and Coldside®, companies can drastically reduce the number of maintenance interventions and extend the operational life of their equipment.
The use of advanced coatings helps maintain low friction levels during the wire drawing process, improving wire smoothness and reducing wear on both the equipment and the processed material. This results in a smoother production flow, higher processing speeds, and superior wire quality. With reduced friction, energy consumption also decreases, leading to cost optimization that becomes evident over the medium to long term.
Another key aspect is the stability of performance over time. Components coated with Paganoni solutions retain their properties even after extended cycles of intensive work, preventing sudden drops in efficiency or failures that could disrupt the entire production line.
Additionally, Paganoni coatings’ resistance to chemical and thermal aggressions ensures a higher level of reliability, which is particularly important in complex processes where traditional materials tend to fail. In short, investing in these coatings not only protects your equipment but also optimizes every phase of the production cycle, turning material quality into a true competitive advantage.
Would you like to discover how to improve your wire drawing plant’s production efficiency? Contact Paganoni today and request a tailored consultation for your facility!
Tangible Benefits of Adopting Advanced Coatings
Adopting advanced coatings for wire drawing components is not just a technical choice; it is a winning business strategy that delivers tangible and measurable benefits. Among the most evident advantages is the increase in productivity: machines that operate for longer periods without interruptions enable higher production volumes and better adherence to delivery schedules, thus strengthening customer trust and enhancing market competitiveness.
Another critical aspect is the drastic reduction in maintenance costs. Thanks to the extended lifespan of components treated with Wolside®, Kerblack®, Kersint®, or Coldside®, the need for frequent replacements or repairs is significantly reduced. This not only optimizes the maintenance budget but also allows for better planning of interventions, avoiding costly and unexpected downtime.
The use of anti-wear coatings also improves the quality of the finished product. A smooth, durable surface reduces friction, thereby minimizing surface defects on drawn wires and increasing the perceived value of the final product in the eyes of customers. In industrial sectors where quality is a critical factor, this can be the deciding point when choosing between suppliers.
Moreover, investing in innovative coating technologies contributes to greater environmental sustainability: by reducing the number of components needing replacement and lowering energy consumption, the overall ecological impact of industrial operations is minimized. This is a significant advantage, especially in an era where environmental responsibility plays an increasingly important role in purchasing decisions.
Would you also like to achieve tangible benefits in your production process? Contact us today to find out how Paganoni’s advanced coatings can transform your results!
YOU MIGHT ALSO BE INTERESTED IN: Innovation in Wire Drawing Materials: Enhanced Performance and Durability
Best Practices to Maximize Component Lifespan
Even with the best anti-wear coatings, the lifespan of wire drawing components can be further extended by adopting specific operational best practices. Paying close attention to everyday details can make the difference between a component that operates in optimal conditions for years and one that requires premature interventions.
A fundamental element is the correct installation of coated components. Improper or imprecise mounting can create abnormal mechanical stresses that, over time, compromise the integrity of the coating and the overall functionality of the system. For this reason, it is advisable to rely on specialized technicians familiar with the specific characteristics of materials like Wolside®, Kerblack®, Kersint®, and Coldside®.
Another crucial aspect is regular monitoring of operational conditions. Checking components only when a failure occurs is not sufficient: preventive maintenance, based on scheduled inspections, allows early identification of wear signs or anomalies. This proactive approach minimizes downtime and significantly extends the service life of equipment.
Cleaning the working surfaces and using suitable lubricants, when necessary, also play a vital role in preserving the anti-wear properties of the coatings. Lubricants must be carefully selected based on the type of material and the specific operational conditions to avoid chemical reactions that could accelerate degradation.
Finally, when wear is detected, it is important to act promptly by opting for professional recovery solutions offered by specialized companies like Paganoni, thus avoiding irreversible damage that would otherwise require complete component replacement.
Would you like to learn how to implement the best practices to maximize the lifespan of your components? Contact Paganoni today and receive specialized technical support!
Conclusions: Investing in High-Quality Coatings for Continuous Production
In an increasingly competitive market, where every hour of production counts, investing in high-quality coatings proves to be one of the smartest choices for companies operating in the metal wire drawing industry. Paganoni’s advanced coatings, such as Wolside®, Kerblack®, Kersint®, and Coldside®, are not merely surface protections: they act as true multipliers of efficiency and reliability for industrial plants.
Choosing technologically advanced materials means drastically reducing the frequency of downtime, improving production consistency, and ensuring a higher quality of drawn wire. The adoption of these solutions also leads to a significant reduction in maintenance and energy consumption costs—key factors today for both the economic and environmental sustainability of manufacturing operations.
The positive impact is also evident in the extended lifespan of components, which require fewer replacements and fewer extraordinary interventions. This enables a more serene and predictable maintenance planning, allowing companies to better protect their machinery investments and increase their responsiveness to the demands of an ever-evolving market.
Opting for high-quality anti-wear coatings is therefore not just a technical decision, but a strategic move that can radically change how a company positions itself against its competitors. With decades of expertise in the sector, Paganoni is the ideal partner for those looking to turn technical reliability into lasting competitive advantage.
Don’t let wear slow down your growth. Contact us and discover how Paganoni’s coatings can help you build a continuous, efficient, and winning production system!