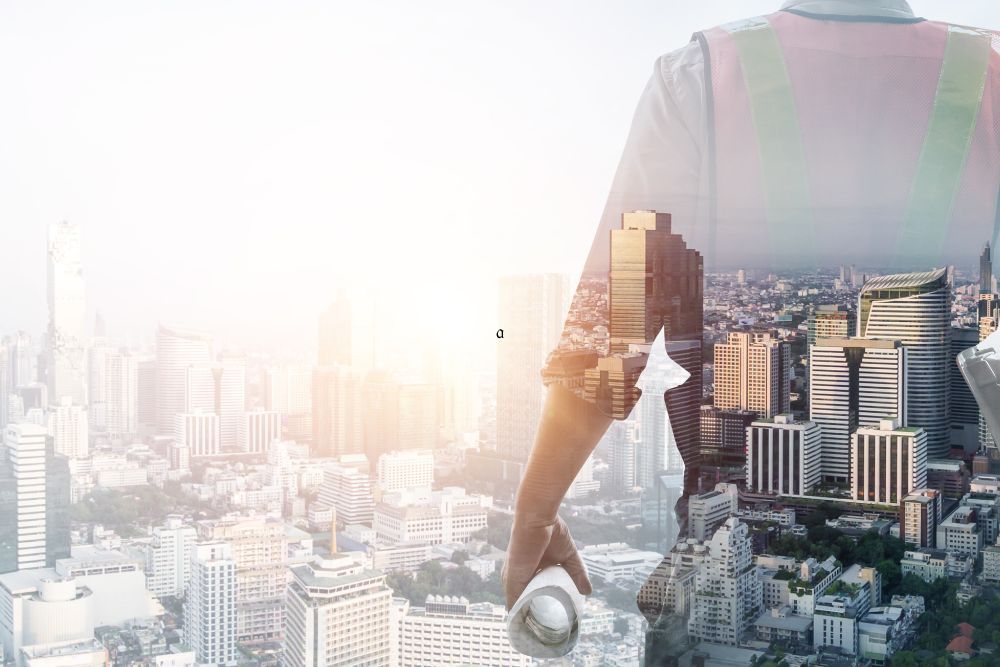
The Future of Wire Drawing Coatings: What to Expect in the Next 10 Years
Why Talk About the Future Today
The wire drawing industry is currently undergoing a transformational shift. The combination of increasingly demanding production requirements, stricter environmental regulations, and emerging advanced technologies requires companies in the sector to rethink the technical solutions they adopt. In this context, discussing the future of coatings is not a theoretical exercise, but a strategic necessity.
Coatings for wire drawing applications play a crucial role: they must withstand extreme wear, friction, and mechanical and chemical stress, while ensuring consistent product quality. Their evolution will directly impact productivity, final product quality, and maintenance costs. The next ten years will be decisive: on one hand, we will witness a push towards the adoption of innovative materials and techniques; on the other, new standards will emerge, redefining performance expectations.
Looking ahead also means being prepared. Companies that begin today to enhance their technical and operational knowledge of coatings will be able to anticipate changes, gaining a competitive edge in terms of efficiency and reliability. With its deep experience and ongoing research, Paganoni represents a benchmark for those looking to innovate with confidence.
Emerging Technological Trends in Coatings
Over the next decade, wire drawing coatings will increasingly feature smart, adaptive technologies designed to respond in real time to the demands of the production environment. The conversation will shift beyond passive wear resistance to functionalized coatings capable of altering their surface properties based on operating conditions.
One especially promising area of research involves multilayer coatings—layered materials with complementary properties that optimize the interaction between the drawn wire and the component surface. These coatings will enable a dramatic reduction in friction coefficients, enhancing smoothness and lifespan. Furthermore, self-healing materials or coatings that release lubricating additives under mechanical stress will emerge to increase component resilience.
Another major trend is the application of nanotechnologies: nanoparticles embedded in the coating matrix offer greater control over surface roughness, adhesion, and thermal conductivity. This translates into faster, more uniform, and more sustainable production.
These innovations will no longer be limited to early adopters. As production costs decline and quality expectations rise, advanced coatings will become the new industry standard in wire drawing. Companies that implement these technologies early will gain a long-lasting competitive edge.
Want to be among the first to adopt cutting-edge coating technologies in your production line? Contact us today to explore Paganoni’s most advanced solutions.
Innovative Materials: From Technical Ceramics to Rare Metals
Over the next decade, the materials used in wear-resistant coatings will evolve significantly, driven by the need for extreme durability, broader application flexibility, and compatibility with increasingly demanding production environments. At the forefront of this transformation are sintered technical ceramics, such as Kersint® developed by Paganoni, which is based on zirconium oxide.
These materials feature exceptional corrosion resistance, particularly in acidic environments, and negligible wear over time—traits that greatly reduce maintenance interventions and machine downtime. Unlike traditional coatings, technical ceramics offer an ideal balance of hardness and elasticity, making them suitable for both dry and wet wire drawing processes.
Beyond ceramics, coatings based on rare metals or composite alloys—as used in Paganoni’s Wolside® and Coldside® products—are gaining prominence. These solutions incorporate tungsten carbides, metal oxides, and nickel in compact or hot-fused forms, which enhance impact resistance and deliver precise surface roughness, essential for high-quality wire output.
The adoption of these advanced materials will no longer be optional but a strategic imperative for companies aiming to optimize productivity and lower the total cost of ownership of their systems. Current innovations signal that the coatings of the future will be smarter, tougher, and more tailored to the specific needs of each wire drawing process.
Looking for cutting-edge materials to extend the lifespan of your industrial components? Request a free consultation with Paganoni’s technical team today.
Automation and Artificial Intelligence in Wire Drawing
In the near future, coatings for wire drawing will no longer be seen as mere protective layers but as integrated components within intelligent production systems. With the rise of advanced automation and artificial intelligence, coated surfaces will be able to communicate with the machine system, providing real-time data about their condition and the surrounding environment.
Sensors embedded in or positioned near coated components will detect micro-damage, thermal fluctuations, changes in surface roughness, and other early indicators of degradation. This data will be processed by intelligent software to trigger predictive maintenance actions—intervening only when necessary, thereby avoiding unplanned downtime and extending component lifespan.
Artificial intelligence, combined with machine learning systems, will also enable real-time optimization of wire drawing parameters based on the actual behavior of the coating. This will result in a more stable, efficient, and customized production process, tailored to the characteristics of each material batch.
Paganoni is already moving in this direction, collaborating with wire drawing machine manufacturers and university research centers to develop coatings compatible with digitized environments. The goal is to deliver solutions that are not only highly wear-resistant, but also smart and interoperable, fully aligned with Industry 4.0 requirements.
Want to learn how to integrate intelligent coatings into your automated systems? Contact us today for a technical consultation on our Industry 4.0-ready developments.
Sustainability and Eco-Compatible Coatings
Environmental sustainability is no longer a trend—it has become a strategic priority for the manufacturing industry, and the wire drawing sector is no exception. Over the next ten years, coatings for wire drawing will be developed according to eco-compatibility criteria, focusing on both the materials used and the methods of application and regeneration.
New coatings will feature formulations free from toxic or polluting substances, with increased emphasis on material recovery and reuse. For instance, ceramic coatings like Kersint®, in addition to delivering high performance, allow for more usage cycles before replacement, significantly reducing industrial waste.
Simultaneously, we’ll see the rise of low-impact deposition technologies, such as optimized sintering and cold spray processes, which minimize energy consumption and greenhouse gas emissions. The component recovery service already offered by Paganoni will play an even greater role, helping to reduce raw material use and overall production costs.
Choosing a sustainable coating won’t just be a responsible environmental move—it will offer tangible economic advantages: fewer replacement interventions, lower disposal costs, and compliance with increasingly strict environmental regulations.
Paganoni is committed to delivering solutions that combine high performance with minimal environmental impact, supporting companies in their transition toward greener, circular production.
Want to make your production more sustainable without sacrificing efficiency? Discover Paganoni’s line of eco-compatible coatings today.
How Coating Selection Criteria Will Evolve
In the coming years, the criteria companies use to select coatings for their systems will undergo a fundamental transformation. It will no longer be sufficient to assess a product solely based on upfront cost or advertised hardness. The focus will shift toward multi-dimensional parameters, including the coating’s impact on the entire component lifecycle and its contribution to the overall performance of the production line.
One emerging criterion will be compatibility with automated and digitized systems, such as integration with sensors and predictive maintenance platforms. Additionally, customization will become a decisive factor: industrial clients will no longer seek off-the-shelf products but instead demand tailored coatings based on their specific processes, wire types, environmental conditions, and production goals.
Another critical aspect will be traceability and performance certification. Companies will increasingly expect verifiable data on parameters like average wear, achieved surface quality, and the dimensional stability of the component over time.
Moreover, ease of component recovery or regeneration will become a key differentiator. Coatings that allow multiple recovery cycles while maintaining consistent performance will be preferred over “disposable” solutions.
Paganoni has already adopted a consultative approach, guiding clients through the most technically appropriate selection process, combining data, field experience, and test results tailored to each industrial requirement.
Are you redefining your criteria for selecting industrial suppliers? Rely on Paganoni’s technical expertise to determine the coating strategy that best fits your production needs.
The Role of Predictive Maintenance
Predictive maintenance will be one of the cornerstones shaping the future of industrial wire drawing. The goal is to anticipate the wear of coated components before it leads to reduced product quality or unexpected machine downtime. This approach relies on the synergy between advanced coatings, smart sensors, and data analytics systems.
By leveraging technologies such as vibration monitoring, thermal analysis, and micro-wear detection, companies will be able to schedule maintenance interventions with precision, avoiding premature replacements or costly delays. Coatings developed by companies like Paganoni are already optimized to be compatible with predictive monitoring, allowing for accurate interpretation of degradation signals.
In this context, not only will downtime-related costs drop significantly, but there will also be a noticeable extension in component service life, resulting in a far greater return on investment compared to traditional maintenance methods. The integration of predictive maintenance with technical coatings will also enable standardization of maintenance procedures, improving production planning and resource management.
Paganoni already supports its clients in adopting predictive monitoring strategies, offering coatings specifically engineered to drive this measurable and effective digital transformation.
Economic Benefits for Evolved Wire Drawing Companies
The adoption of advanced technical coatings will bring measurable and long-lasting economic benefits to wire drawing companies ready to evolve. In a market where operational margins and productivity are under constant pressure, any solution that improves efficiency and cuts costs becomes strategically vital. Next-generation coatings—like those developed by Paganoni—represent high-yield investments that deliver value on multiple fronts.
The first direct benefit is the reduction in maintenance costs. With increased wear resistance and longer component lifespan, expenses related to replacements, downtime, and labor are significantly lowered. This is accompanied by improved production continuity, which helps companies meet deadlines, enhance delivery schedules, and increase customer loyalty.
Another key advantage lies in the consistent quality of the final product. The surface finish of drawn wire remains stable for longer periods, reducing waste and increasing the volume of sellable output. This directly translates to economic savings and heightened market competitiveness.
Moreover, the use of regenerable coatings—compatible with Paganoni’s component recovery service—further reduces costs by extending the life of capstans, cones, and pulleys without sacrificing performance.
In short, for forward-thinking companies, investing in technical coatings offers a clear economic advantage, positively impacting the entire production chain.
Want to estimate the return on investment from Paganoni’s advanced coatings? Contact us now to receive a customized economic analysis for your facility.
Paganoni: Solutions Ready for the Future
In today’s increasingly complex industrial landscape, anticipating change is key to staying competitive. With over fifty years of experience in wear-resistant coatings for wire drawing, Paganoni stands as a trusted partner for companies seeking to face the future with proven, ready-to-deploy solutions.
The company has continuously evolved by integrating research, development, and customer feedback into a broad, technologically advanced offering. Products like Wolside®, Kerblack®, and Kersint® are more than just coatings—they are strategic responses to the major challenges of modern wire drawing: accelerated wear, poor wire quality, frequent downtimes, and maintenance difficulties.
Each Paganoni solution is the result of rigorous testing, real-world application trials, and customization based on specific client needs. The company also offers a recovery service, which significantly extends the life of worn components, delivering both economic and environmental benefits.
What truly sets Paganoni apart is its role as a technical partner, providing a consultative, results-oriented approach combined with a vision of continuous innovation. The goal isn’t merely to sell a product, but to help redefine the overall efficiency of the production process.
For companies looking to prepare for the challenges of the next decade, Paganoni offers not only advanced technologies but also an ecosystem of expertise, services, and forward-looking solutions.
Conclusion: Wire Drawing in the Next Ten Years
The wire drawing industry is set to undergo one of its most significant transformations over the next decade. This change will be driven by the need for production efficiency, increasing environmental pressures, and the rise of digital technologies. In this evolving landscape, technical coatings will become a core element in optimizing the entire industrial process.
The focus will not simply be on selecting more resistant materials, but on adopting smart, customizable, sustainable, and digitally compatible solutions. Future coatings will be able to communicate with machinery, self-diagnose wear, be regenerated with minimal environmental impact, and continuously enhance operational performance.
Companies that anticipate this shift will gain a tangible competitive advantage: lower operating costs, greater reliability, consistent product quality, and a strong reputation built on innovation and environmental responsibility.
Paganoni positions itself as the ideal partner to lead this transition, offering a range of future-ready coatings, highly specialized technical support, and a strategic vision for the role coatings will play in tomorrow’s industrial wire drawing.
Investing in this direction today means positioning your company to lead the market of tomorrow.
Ready to take your company to the next level in wire drawing? Contact Paganoni now and start your journey toward high-performance, sustainable innovation.